SUCCESS STORY
Curtiss-Wright: Enhancing Manufacturing Efficiency with Real-Time WIP Tracking
Curtiss-Wright revolutionized its manufacturing operations with Xemelgo’s real-time WIP tracking solution, gaining instant visibility into production and dramatically reducing lead times. By eliminating manual searches and streamlining material flow, the team accelerated order processing, minimized inventory levels, and empowered employees with actionable insights—driving efficiency across their complex operations
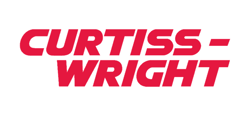
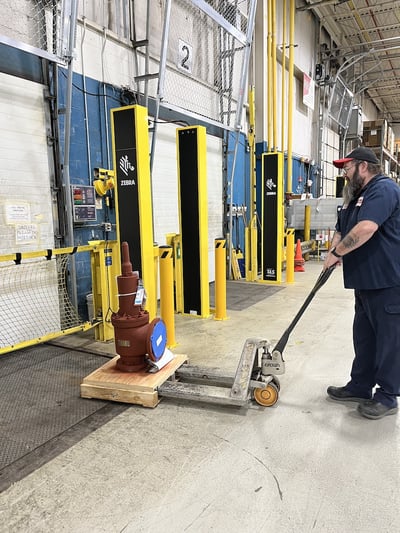
RFID has transformed the way we manage our WIP. Being able to review orders with real-time tracking allows planning and operations to quickly identify problematic orders, helping us maintain our deadlines to increase on-time delivery and customer satisfaction.
Outstanding results! Our shop floor’s Work-In-Process (WIP) has been significantly reduced by 90% enabling faster product delivery to our customers and more efficient use of time for our expediting team.
I have nothing but compliments for all parties involved. This has been the smoothest integration and implementation I have ever experienced — everything went smoothly.
Learn About How Curtiss-Wright Accelerated Production Orders with Xemelgo
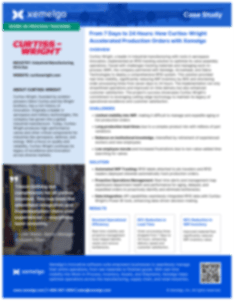
Curtiss-Wright, founded by aviation pioneers Glenn Curtiss and the Wright brothers, has a rich history of innovation. Originally a leader in aerospace and military technologies, the company has grown into a global industrial manufacturer.
Today, Curtiss-Wright produces high-performance valves and other critical components for industries like aerospace, defense, and energy. With a focus on quality and reliability, Curtiss-Wright continues its legacy of excellence and innovation across diverse markets.
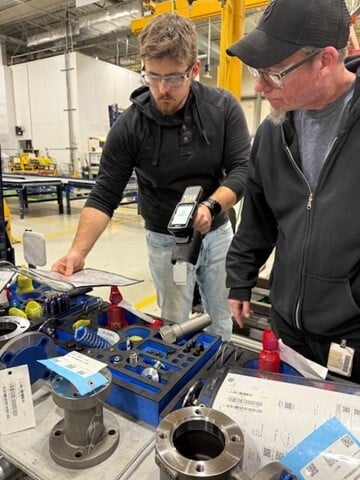
Curtiss-Wright's reliance on manual processes made it difficult to pinpoint the exact location and status of WIP items:
-
WIP Blind Spots
Lack of real-time insight into WIP made it challenging to prioritize urgent or delayed production orders. -
Complex Product Mix
Extended lead times driven by a highly complex product mix with millions of possible part combinations. - Knowledge Gaps
Heavy dependence on tribal knowledge, further strained by the departure of veteran staff and onboarding of new team members.
- Low Morale Drivers
Employee frustration and reduced morale caused by excessive time spent locating valves instead of performing value-added work
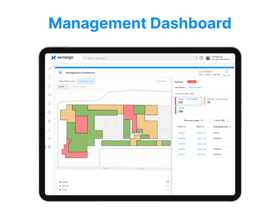
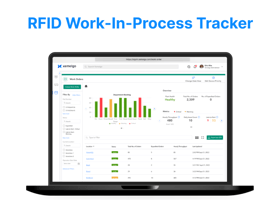
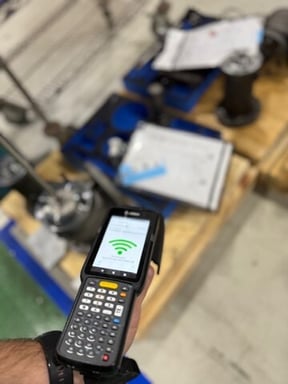